
Groupe Beneteau introduces ‘closed loop’ process to decrease impact of boatbuilding
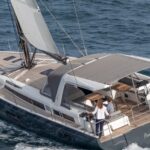
An alliance of six global industry leaders, including Groupe Beneteau, has collaborated to introduce a new ‘circular economy’ model for boat manufacturing, which incorporates recycled materials into production.
The closed loop boatbuilding initiative lays the groundwork for boats built from recycled materials to reduce their overall environmental impact — particularly at end-of-life.
The collaboration, launched in France, involves multiple companies: boatbuilding giant Groupe Beneteau; Veolia, a specialist in waste management and environmental services; Composite Recycling, focused on composite waste recycling; Arkema, a producer of specialty materials; Owens Corning, known for glass reinforcement innovation; and Chomarat, a supplier of technical textiles and composite reinforcements.
End-of-life vessels are in the spotlight across the industry, with mounting concerns about how to handle boats once they reach their natural end. In January, the International Council of Marine Industry Associations (ICOMIA), European Boating Industry (EBI), and National Marine Manufacturers Association (NMMA) joined forces to develop a global recreational marine lifecycle assessment (LCA) framework. This collaboration established the first-ever global partnership to assess, measure and report the industry’s environmental performance of recreational boats.
And, in July 2024, a British study discovered a ‘disturbing level’ of fibreglass in oysters and mussels. The authors noted that for the first time, fibreglass or glass-reinforced plastic (GRP) particles were found entering the food chain, raising urgent environmental and health concerns related to discarded boats.
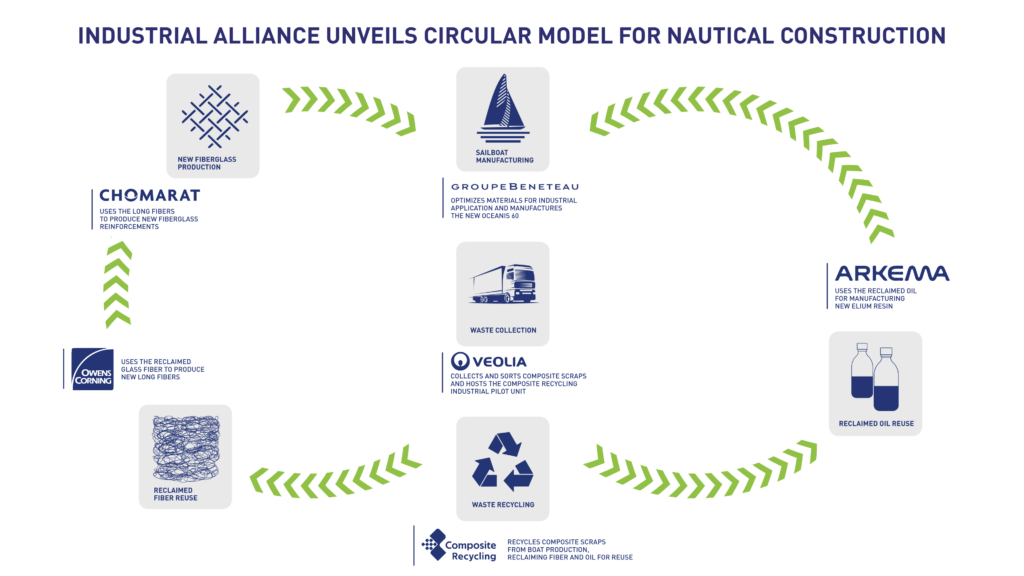
The collaboration, launched in France, involves multiple companies working together.
How does ‘closed loop’ boatbuilding work?
The closed loop boatbuilding process involves Groupe Beneteau integrating recyclable composite materials, including Arkema’s Elium resin, into boat production.
Elium resin is a multipurpose liquid thermoplastic resin used to make composite parts. It’s made by Arkema and is based on methyl methacrylate (MMA) and acrylic copolymers. Elium can be processed at ambient temperatures with short setting times and, crucially, is recyclable as it can be separated into fibres and reused.
Veolia then collects production scraps for recycling at its western France facility. Composite Recycling applies thermolysis technology to separate materials, producing reclaimed glass fibres and thermolysis oil. Arkema then converts the oil into new Elium resin, while Owens Corning manufactures new glass fibres and Chomarat develops fresh fibreglass reinforcements. These materials are then reintegrated into new boats, completing the cycle.
Erwan Faoucher, vice president of innovation and sustainable development at Groupe Beneteau, says: “This collective approach is a decisive step in our commitment to accessible and sustainable boating. Our Jeanneau Sun Fast 30 One Design models and, more recently, Beneteau Oceanis Yacht 60 perfectly illustrate that circular manufacturing in the nautical sector is no longer a simple goal, but a tangible reality.
“Once again in our history, we are showing audacity. The use of recycled resin reduces CO2 emissions by 70 per cent compared to conventional polyester from the market. Whereas in the past we made boats that were built to last, today we are able to design sustainable boats.”
While this approach has applications for sustainable boatbuilders, its proof of concept extends beyond the marine industry, and has potential applications in other industries that use composites, such as automotive, aerospace, wind energy and construction.
Guillaume Cledat, Arkema global business manager, says: “Elium resin was designed to make composites recyclable, and this initiative showcases how it works at scale. By combining Elium resin with innovative recycling technologies, we’re laying the foundation for a circular economy in composites.”
Guillaume Perben, co-founder of Composite Recycling, adds: “Sailing has always been a part of my life, so I’m especially proud that the first application of our industrial unit is within the marine industry. But this isn’t just about sustainable boatbuilding—it’s a proof of concept for every industry that uses composites.”
In a joint media statement, the six participating companies say they aim to refine the process from here, and explore further industrial uses to reduce waste and lower environmental impact across multiple industries.
The post Groupe Beneteau introduces ‘closed loop’ process to decrease impact of boatbuilding appeared first on Marine Industry News.