
Sleipner: Why keeping processes in-house is ‘well worth it’
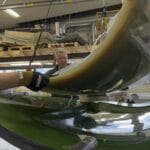
Sleipner, the Norwegian technology-driven company, known for its industry leading thrusters and stabilisers, is fielding projects with leading boat manufacturers and is busy anticipating how the electric revolution may impact its clients and products.
Along with a new headquarters, scheduled to open in 2025, this era is proving pivotal for the company.
Thomas Skauen, product communication manager for Sleipner, says: “Our innovations and focus are deeply rooted in practical experience. With Norway boasting one of the highest boat densities per capita globally, it’s no surprise that many of our employees are avid boaters. This firsthand experience is a priceless asset in all aspects of our operations. Our team’s intimate knowledge of the importance of reliable equipment onboard drives us to design, build, and test our products to the highest standards.
“We choose not to diversify our product range too much but instead concentrate on perfecting what we do best. Achieving this goal has taught us that any process we can keep in-house within acceptable economic limitations is well worth it. Not only do we build vital technical competence in many areas within the company, but our boatbuilder customers need to provide their customers with the best quality solutions for their overall boat experience. Keeping processes in-house allows us to be in total control of every quality checkpoint ourselves.”
Blueprint for boatbuilders
Sleipner works with a host of leading builders, from Princess, Sunseeker, Fairline and Ferretti Group to Axopar, Windy, Hallberg-Rassy and Beneteau Group.
“We recognise that builders and suppliers exist in a symbiotic relationship, we all benefit from each other’s success,” explains Skauen.
“Being a technology-driven company, we get asked to participate in many joint development projects with boatbuilders. As you can imagine, there are a lot of NDAs involved in our work but what is true to say is that over the last few years we’ve been involved in many projects around electrification with various boatbuilders.”
On occasion, the Sleipner team has been called in to work on big projects where a builder is trialling something totally new or working on a drastically new design, but Skauen says the team is most often required to tweak one of the Sleipner components to fit or adapt to a space or limitation. “Because space aboard is always the issue, right?”, he adds. “There is always too little of it. And that’s also why we now have this humongous range. I think we have about 350 thruster models – and that’s a direct result of brands coming to us and asking us to adapt them to their boat.
“A major benefit for us is the feedback we get from these collaborations. We like to think of the customers more like partners, or we want to have that relationship with them because when we achieve that level of collab our team gets to understand more of the builder’s bigger picture.
We can appreciate what those builders are planning for next year, or three years ahead. So we, in turn, know what we need to do, what inventions we need to mastermind to keep inline with client plans.
“We’ve seen this in the evolution of dashboards, for example. Compared to ten years ago, users now like to have integrated information from our systems on the multifunction displays that now dominate boat dashboards. And so, we facilitate this to move with the times.”
As its portfolio has increased with larger systems and more products now approved for classed vessels, Sleipner has seen expected growth in deliveries to larger yachts and the commercial sector.
Having optimised the hydraulically driven Vector Fin stabilisers for about 15 years, the recently launched electric version is seeing a lot of interest from existing and new customers as well.
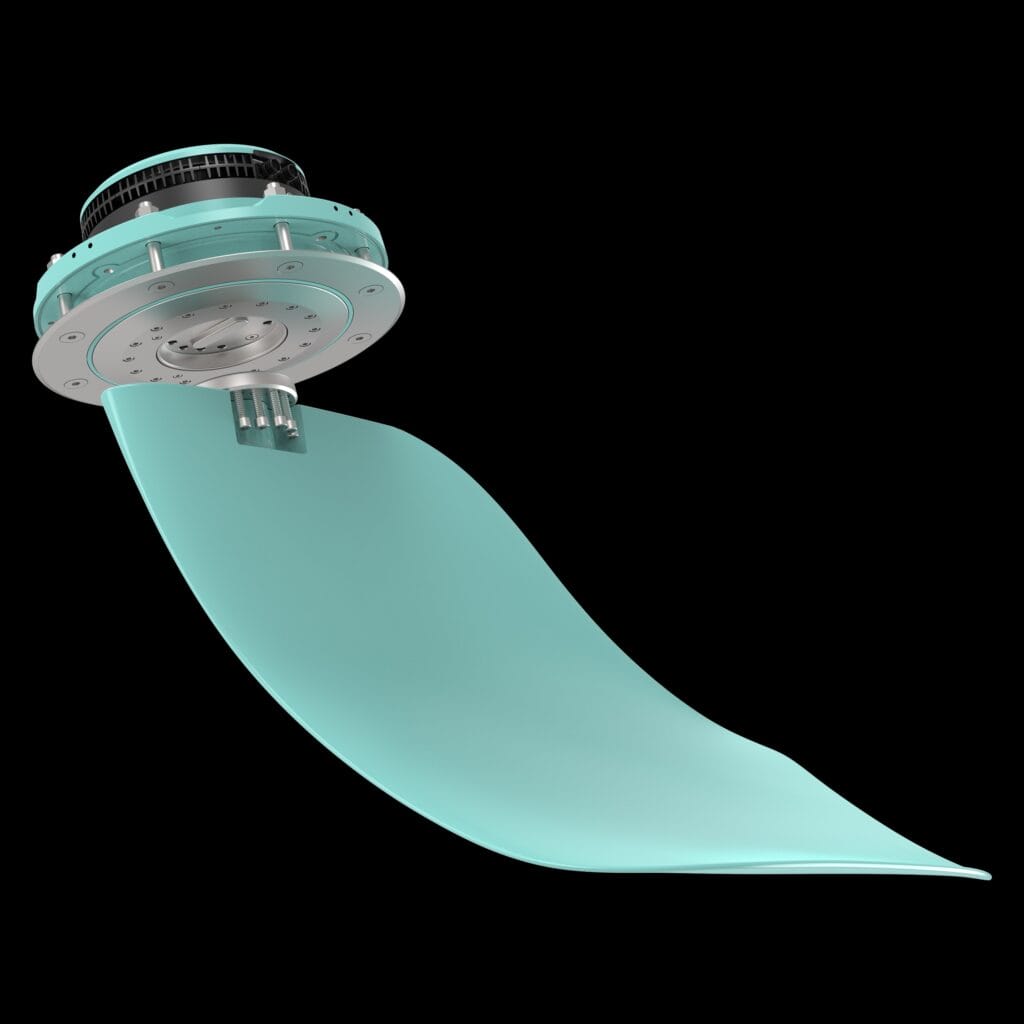
According to Sleipner, the patented curved fin design is significantly more effective than flat fins, an attribute more and more builders are actively seeking to reduce the overall consumption and dimensions of their onboard power systems. The company is also launching larger thruster models and a new series of AC electric thrusters that are smaller and lighter than standard models.
Sleipner E Series
Sleipner’s E Series is produced in Norway. This is the first time since the 1970s that the company will be manufacturing its own motors. The company has made a significant investment in new production facilities to build the electric motors, with robot/automation technology, new CNC machines and full production line.
While the E Series currently accounts for a small part of the business today, this outlay is a way of futureproofing Sleipner’s steps into electrification. Skauen says the move readies the company to gain more of a foothold in this sector as adoption and wider use and projects arise.
“In a way, those motors are overkill, to be honest, because the technology used rivals the design technology we see in the electric car industry, for instance. And obviously for leisure boating use, you don’t need such advanced tech. But for joystick integrations and dynamic positioning systems that are in the pipeline, and commercial vessels that require longer run times, you can run these motors forever.
“From a singular perspective, it doesn’t make a lot of sense to invest so much in R&D and set up a production line and so on for, let’s say, 50,000 motors. But the know-how gained from this project is invaluable. We believe that we will see more electrification and more hybrid solutions in the future in boating. Thus, the strategy behind building a full factory line for the E Series is rooted in longer term thinking. It is about how we can perhaps help or find our place in the industry within that process.”
The economics of manufacturing in Norway
Sleipner produces almost all of its products across its sites in Norway, apart from some GRP parts, which are manufactured at a fully owned Polish factory. “It’s always fun to take people on a factory tour because they are really surprised that we can do all the things we do inhouse in Norway and still be competitive.
“A lot of people think that Norway is so expensive and that it’s almost impossible to produce anything here. Maybe we’ve been lucky with our investments but we have always also invested in modern machines. A milling machine, for example, costs the same in China or in Italy or in Norway to purchase. So if you have a hugely effective machine, then if the employee operating it costs a little bit more per unit, it’s very little in the long run.
“That’s been our philosophy – if we can invest in the latest and best production technology, we can produce it in Norway, even though it’s a higher cost country to produce in.”
On water lab
While Sleipner does currently have some test stations on rivers, this still involves labour intensive and costly transportation of huge test rigs to the rivers. It makes sense, therefore, that the company has opted for its new factory and HQ to be built on the water. The new HQ will feature a state-of-the-art test lab where the Sleipner team will be able to test easily and exhaustively on the water.
“Our new HQ is really exciting. It’s actually a very small site compared to what you could opt for in an industrial area where you can get a much bigger plot but we wanted to be by the water because the testing part of our business is critical. And if we can test on site to figure out flaws, it’s much cheaper to test and resolve it here.”
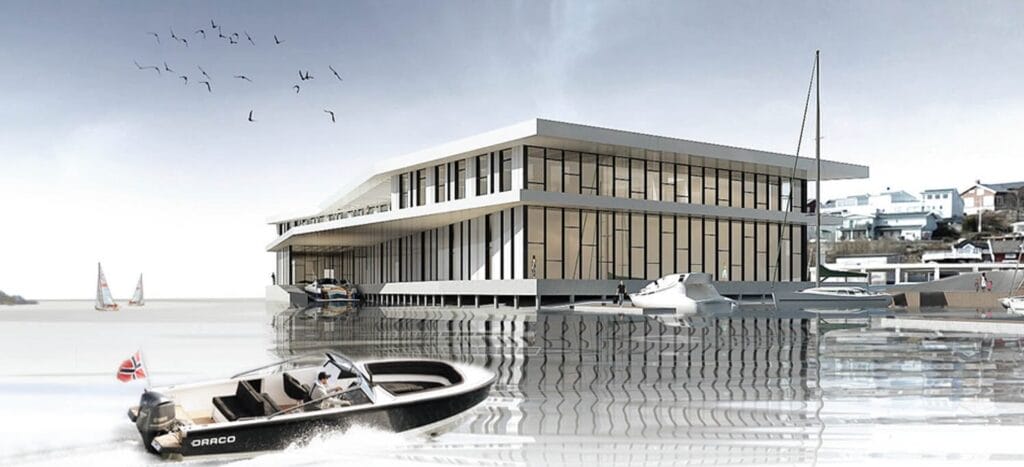
The new 12500m² HQ will house offices, R&D facilities, the test lab and manufacturing, whereas warehouse and shipping facilities are located at a neighbouring logistic hub that opened in 2023.
“Having that test lab out over the water means that we can put the products straight in the water and let them run for as long as we need to.
“Also I think that having many of the production departments – at least the most difficult or challenging ones – together with engineering departments and test station will make it so easy for those departments and teams to talk and gather information without going around a lot of different locations.”
The company is hoping the HQ to be open by end of 2025. When the new HQ and test lab opens, the Poland GRP factory will still remain in action. “We are working on some pretty cool technology – some of which isn’t even around yet. So we do foresee that we will need a lot more space for some new product lines. It’s a bit too early to go into specifics – maybe next year we will be able to share a bit more about what we are up to.”
The post Sleipner: Why keeping processes in-house is ‘well worth it’ appeared first on Marine Industry News.